Formlabs Fuse 1+ 30W & Sift SLS Printer
The hugely respected desktop 3D printer manufacturer, Formlabs, has recently launched a second Selective Laser Sintering (SLS) system, the Fuse 1+ 30W. Reaching levels acceptable for industrial applications, the Fuse Series of benchtop printers incorporate every easy-to-use hardware and software option available to give the user a highly efficient SLS 3D printer.
The Fuse 1+ 30W prints in an ever-increasing range of powders, including Nylon 12, Nylon 12GF, Nylon 11 and the latest – Nylon 11 CF. Each one offers individual advantages but collectively each will ensure parts that have high environmental stability and strength, with ideal features for functional prototypes and parts with complex geometries.
Key Features
The new Fuse 1+ 30W has been fitted with a laser 3x more powerful than that on the Fuse 1, resulting in a printing speed that is 2x faster.
New to the Formlabs range, and only available on the Fuse 1+ 30W, is the Nylon 11 CF material. Exhibiting stiffer properties the Nylon 11 CF is suitable for more end-use applications.
Formlabs has introduced a nitrogen purge option on the Fuse 1+ 30W. The advantage of this input means better quality parts, lower refresh rate and lower part costs.
A better than 30% material refresh rate means you can print with up to 70% recycled powder, indefinitely. Fuse Sift’s sieve filters out particles to be remixed with new powder and reused in future prints.
A negative air pressure system within the FUSE Sift keeps powder inside while enabling open access and easy cleanup.
Fuse Sift will dispense and mix used and new powder automatically so you can reduce waste and control your powder supply.
Reduce downtime by transferring modular build chambers and powder cartridges between the Fuse 1 and Fuse Sift for a nonstop, cyclical workflow.
The Fuse Sift includes a set of finishing tools to help you clean excess powder from parts with ease.
Powder recovery
After the part is built, recovery of the powder is by vacuum extraction in the Fuse Sift recovery station. This unit is separate to the printer and ensures maximum safety in the environment containing the powder. The required operational level of the anti-static dissipative vacuum is NFPA 652 – Class II Division 2. Using accessories such as the hose, the vacuum can also be used to clean the build chamber and sifter mesh as well as keeping the general area clear of loose powder.
Powder cartridge
To enable continuous printing, it is possible to transfer the powder cartridges and build chambers between the Fuse 1+ 30W 3D Printer and the Fuse Sift recovery station. Powder from the Fuse Sift can be recycled into the Fuse 1+ 30W hopper, with the powder cartridge doubling-up as a mixing container to combine the new and recycled powder.
Safe and efficient powder recovery.
Fuse sift combines filtration and powder recovery in one machine. This system enables you to produce fully functional parts with a 30% powder refresh rate -with unlimited cycles, meaning printing can be done using 70% of recycling materials. Pack as many parts as possible into the build chamber for maximum throughput.
Easy post-processing for SLS
The Fuse 1 and Fuse 1+ 30W represent the most functionality offered by an SLS system on the market. They can extract and mix used sifted powder and fresh powder together, as well as store, dose and refill the powder cartridge ready for use. Fuse Sift can recycle a greater amount of used powder that makes your processes faster while minimising the risk of contamination.
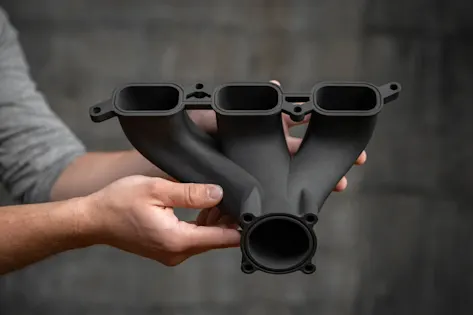
Reduce post-processing time
Building parts as complete assemblies reduces the time spent on removing the powder in the Sift. It will also reduce the time involved to post-process the parts.
More volume, More parts
Selective laser sintering gives users free access to the entire build volume without needing any space for supports because the powder supports the parts independently. With a maximum build size of 15.9 x 15.9 x 29.5 cm, the Fuse 1 allows for quick production of multiple components.
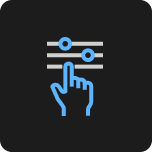
Intuitive
The Fuse 1+ 30W is designed for minimal upkeep. A full colour touchscreen interface guides you through every step of printing and maintenance.
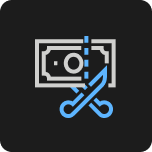
Affordable
With reduced equipment cost, affordable material, and efficient powder recycling, the Fuse 1 is the smart choice for industrial quality SLS 3D printing.
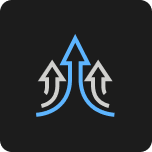
Efficient
From print setup to powder recovery, our easy-to-use hardware and software are designed to maximize your efficiency at every step of the process.

Fast, simple print setup.
Use Formlabs PreForm print preparation software (free to download and try) to import STL or OBJ part files, orient and arrange models, estimate print times, monitor your printers, and upload job files.
PreForm’s part packing algorithms can automatically arrange multiple models in a build.

Compact Selective Laser Sintering made manageable
During setup and printing, an intuitive Touch UI walks you through every step.
The touchscreen displays a live stream of the print bed so you can watch each new layer take shape. This camera view is also available from your computer in PreForm so you can monitor your print without leaving your desk.
Track printers, teams, and supplies via the cloud-based Dashboard.

Reliable, consistent printing.
Selective Laser Sintering 3D printing fuses nylon powder layer by layer. The unused powder supports the parts during printing so you can create complex, interconnecting designs with no need for support structures.
With patent pending Surface Armor technology, a semi-sintered shell that prints around the surface of the part, the Fuse 1+ 30W provides competitive mechanical properties and surface finish without the prohibitive cost or hassle of competitor systems.

Safe, efficient powder recovery.
Our all-in-one powder recovery station, Fuse Sift, combines part extraction, powder recovery, storage, and mixing in a single device.
Produce fully-functional parts at a 30% powder refresh rate—with unlimited cycles. This means you can print with up to 70% recycled powder.
Fuse Sift will dispense and mix used and new powder automatically so you can reduce waste and control your powder supply.